Modernizations
The Economical Alternative to a New Purchase
The provision of maintenance and innovative modernizations – over decades and for all machines delivered by WaldrichSiegen – is the core of our business. This includes the comprehensive and prompt supply of spare parts along with complete revamps of our machines. We also modernize third-party products. After 10 to 15 years of operating time, a modernization of machine controls, measuring devices and drivers is recommended. The availability of electronic parts are limited from suppliers over time.
Cost-Efficient Alternative
Basically, even after decades of intensive machine use a complete revamp can be an effective and cost-efficient alternative to new investments. We carry out the revamp process either at your site or at our facilities. A revamp will update your machine to state-of-the-art performance – and provides you with considerable economic benefits due to optimum machine performance and machining results.
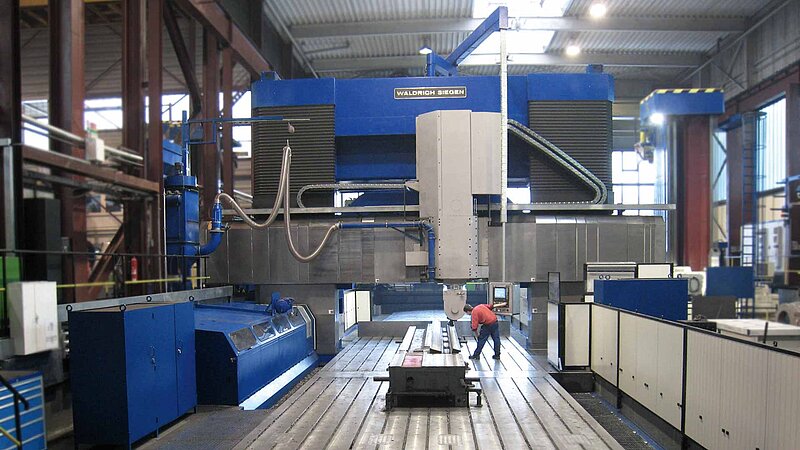
Teleservice
Reliable Remote Service
For machines of the current scope of supply, and for selected revamped machines, our specialists offer remote diagnostics through teleservice as an option. An undisturbed data transfer between machine and service technician is the precondition for smooth running of the teleservice.
The Advantages of Teleservice:
- Reduced downtimes
- Increased operational availability
- Reduced long-term operating costs
- More efficient and faster fault diagnosis and resolution as well as purchasing of spare parts
- Reduced service costs after the warranty period
- Reduced costs for maintenance specialists
- Bridging language and cultural barriers
- Increased internal problem-solving capacity
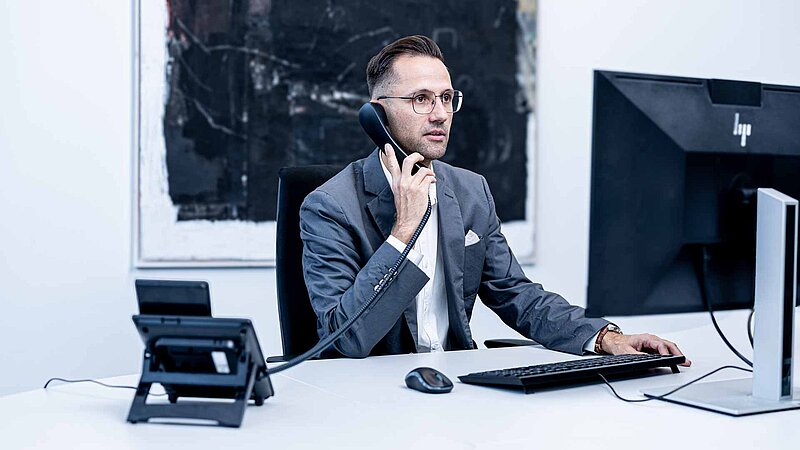
Training Worldwide
Know-How From Experts
Well-trained employees play an important role within the company as well as in the production. To guarantee the faultless operation of our machines in your company, and to minimize training time, we offer trainings that go beyond operational and programming training.
Targeted and Efficient
Our instructors teach their specific know-how of the efficient application of our boring mills in your production in a goal-oriented and individual way.
In addition to training for operators and programmers, we offer the following contents:
Service and Maintenance
- Electrics
- Mechanics
Application
- Machining your own workpieces
- Cutting
- Time studies
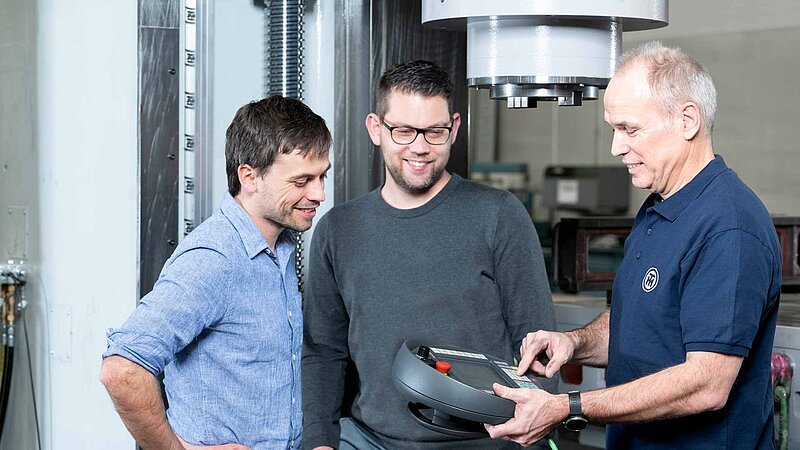
Application Technology
Expert Advice From the Get-Go
The specialists of the HerkulesGroup offer comprehensive technological advice from the very beginning. Our experienced application technicians develop optimal machine configurations for the application in your company – including tool and clamping concepts.
Service From the Outset
We offer on-the-job training on the machine for your maintenance personnel (mechanical/electrical), operators and programmers, to take place either at our location during pre-acceptance or at your facility. This guarantees a smooth integration and operation of the machines in your facility and reduces the run-in period to a minimum.
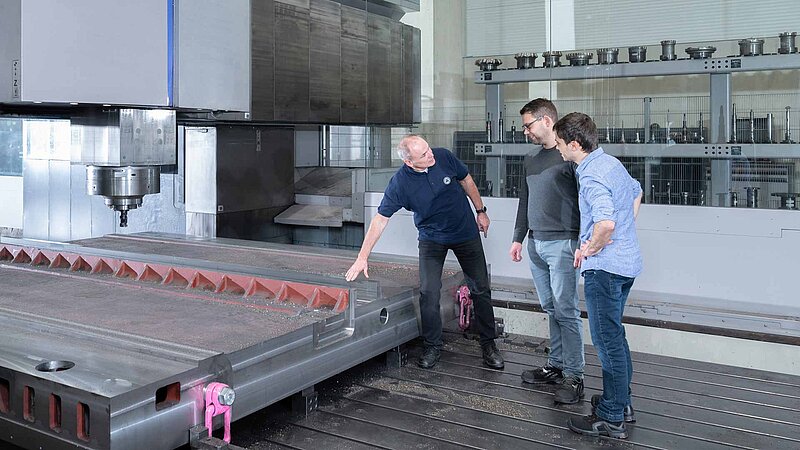
Global Presence
We have set up a worldwide sales and service network. Our service departments in Germany, China, India and the United States will assist you with the on time supply of spare parts and machine components, with maintenance at regular intervals, simple to complex repair works, as well as, with complete installations of new machines.
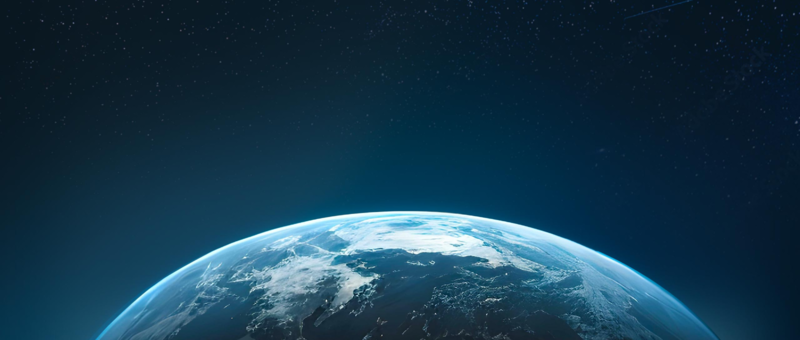
Your Contact Persons
In line with our philosophy, we offer our customers the best possible service over the entire life cycle of the machine - from the initial project inquiry through to modernization decades later. Our trained sales staff and application engineers will provide you with comprehensive advice and develop a customized machining strategy that is perfectly tailored to your needs.
Oliver Klein
Sales spare parts
57074 Siegen
- +49 271 6906-428
- oliver.klein@ herkulesgroup.com
Stephan Mager
Customer Training
57074 Siegen
- +49 271 6906-189
- Stephan.mager@ herkulesgroup.com
Contact
UNION Products
Marcus Quentmeier
Service UNION
04610 Meuselwitz
Germany
- +49 3448 83129
- +49 160 96658662
- marcus.quentmeier@ herkulesgroup.com