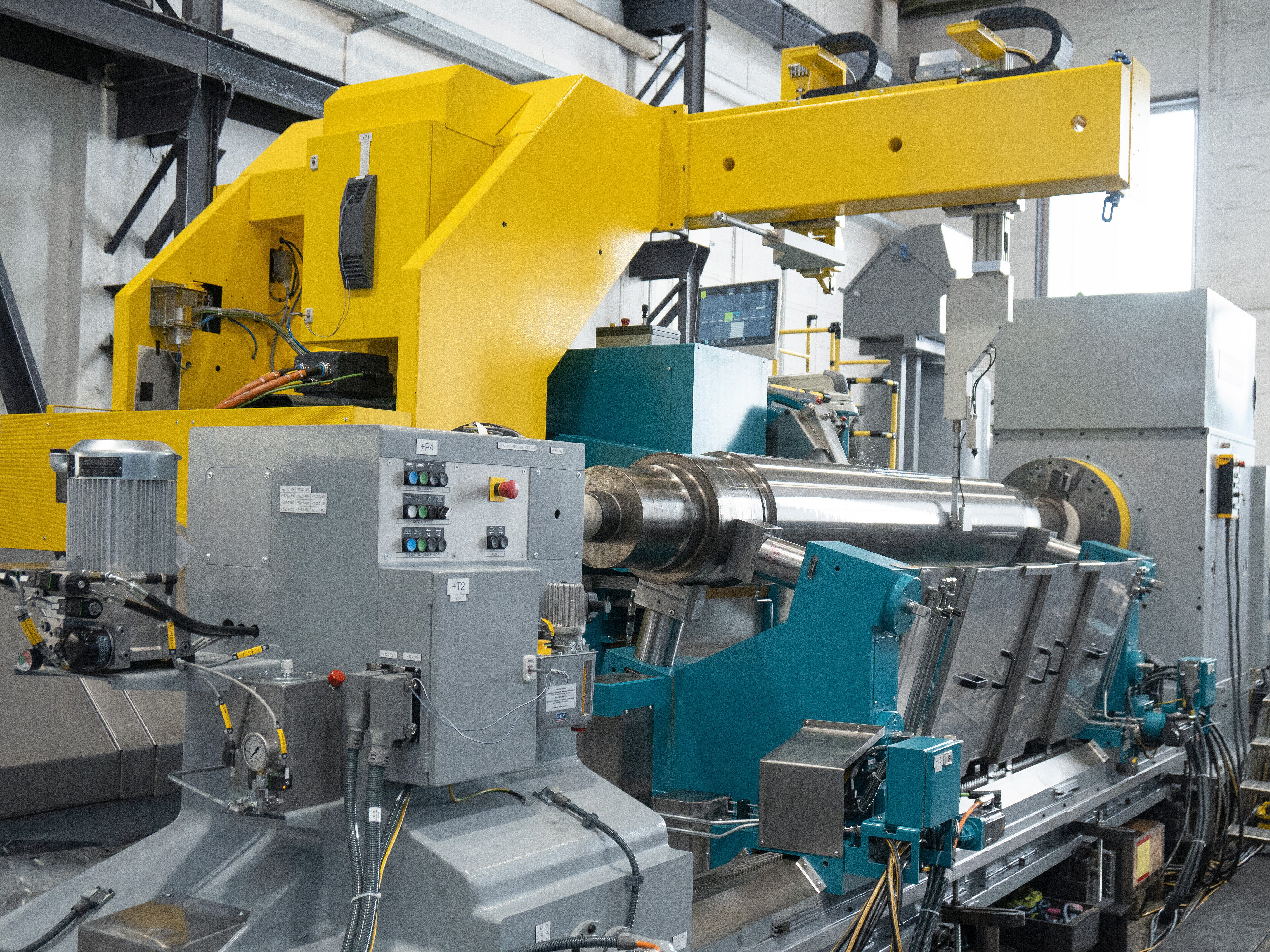
WaldrichSiegen Wins the "Golden Ticket"
on the Steel Market in Japan
For the expansion of their steel mill, a Japanese customer has ordered a fully automated roll shop with a total of six ProfiGrind roll grinders, thereby awarding one of the largest and most important steel mill projects in Japan in recent years to WaldrichSiegen.
"Thanks to our long-standing cooperation with Primetals and the excellent reputation of our machines and services in Asia, we were finally able to sign the contract, which is a great success for us," explains Jannik Schneider. For grinding the rolls in chocks from the hot rolling mill, Primetals has purchased four ProfiGrind 2500 work roll grinding machines. These grinders take work rolls and machine them up to a total length of 6,500 mm, a diameter of 65 to 900 mm, and a workpiece weight of
25 t.
"With two additional ProfiGrind 5500 universal roll grinders, it is now possible to additionally machine back-up and intermediate rolls with and without chocks with a roll length of up to 7,000 mm and a maximum weight of 55 t," explains Jannik Schneider. Another special feature is that, in addition to conventional grinding, smaller turning operations can also be carried out on new rolls thanks to the turning tool holder. All machines are also equipped with HCC/KPM's excellent measurement and control systems.
To minimize downtime in the rolling mill, it is important to detect defective rolls at an early stage. Cracks and other defects near the roll surface, that cannot be seen with the naked eye, are reliably detected with HCC/KPM’s outstanding surface inspection technology (Eddy Current and Ultrasonic). The Eddy Current measurement reliably locates open cracks and changes in the roll’s microstructure. Since the Eddy Current sensor is integrated into the roll measuring system, all measurements take place “on the fly” and thus without loss of time. A separately running Ultrasonic inspection detects manufacturing and fatigue defects inside the roll.
The horizontal alignment of the roll can be accurately determined with the aid of the CP measuring arm for fully automatic measurement of the roll geometry. The calibration ring also enables accurate centerline alignment and an absolute diameter reference.
The fully automatic roll shop also includes two automatic loaders with a loading capacity of 25 t for loading and unloading the ProfiGrind 2500 work roll grinders. Both loaders operate simultaneously in the automated zone with travels of 97 m in length and 20,1 m in width and are controlled and monitored by the MRS. In addition, the loaders can rotate the chocks of the rolls by 90°.