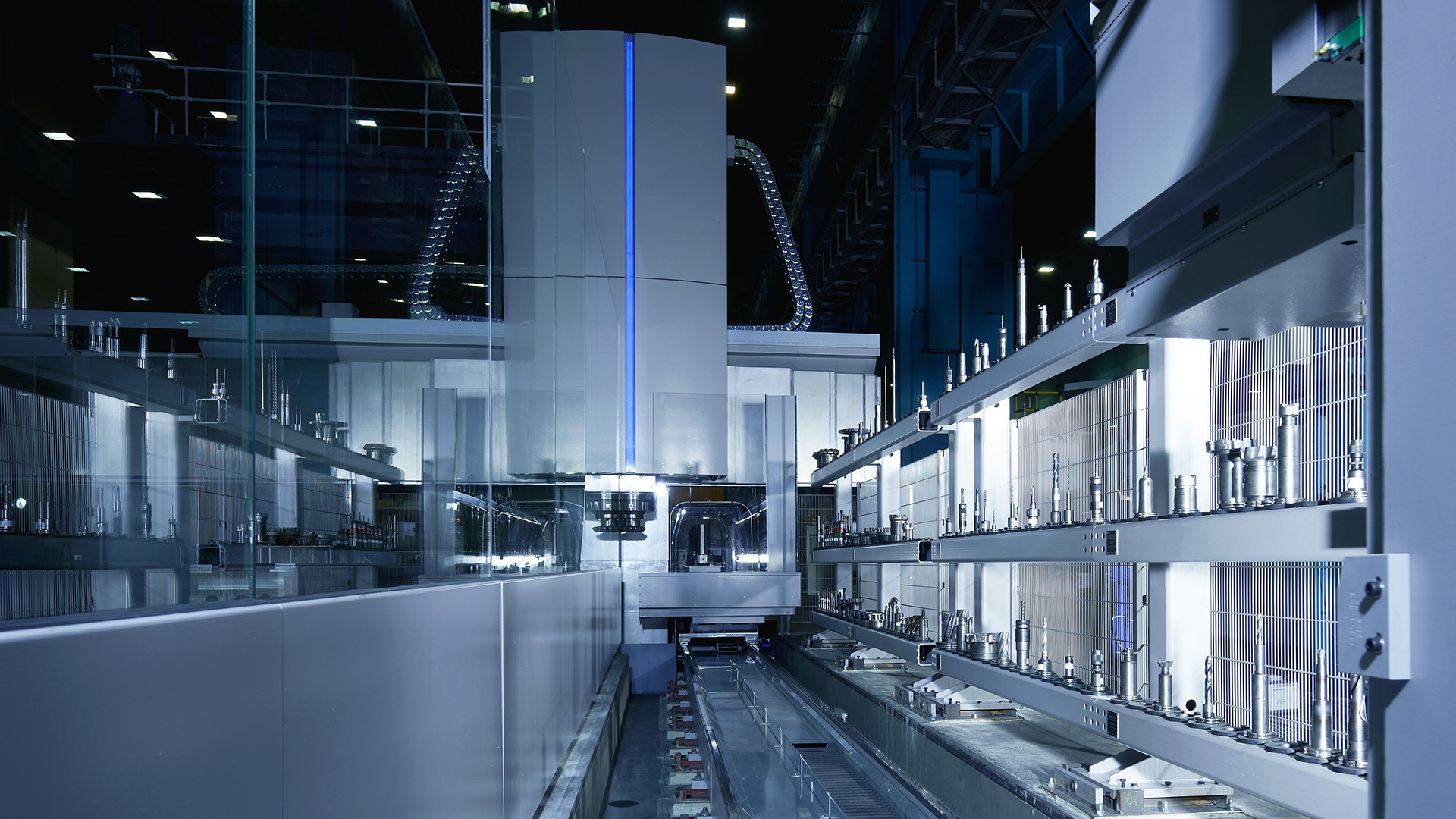
Intelligent Turnkey Manufacturing System for Sustainable Production in the Smart Factory
Based on a trade show contact from 2019, we were able to win KraussMaffei Technologies GmbH from Munich as a new customer for an order of two fully ProfiMill 4500/103-TP portal milling machines with pallet changer and flexible manufacturing system.
For the production of injection molding machines with a clamping force of up to 6,000 t, powerful, robust and highly precise machine tools are required for the machining of large components. Therefore, both machines with a length of 25.30 m each are designed with fully hydrostatic main axes. Despite the impressive dimension of more than 70 m total total length of the machining center and a milling power of more than 100 kW, both machines convince with highest long-term accuracy in the machining of plane surfaces (0.02 mm) and column bores (≤ 0.01 mm) as well as a flexible and fully automated machine concept developed especially for our customer.
However, it was not only the high outputs and continuous accuracies that were convincing - above all, the smart overall concept and the productivity of the entire plant in conjunction with the high energy efficiency of the production, had a decisive influence on the purchase decision. WaldrichSiegen is rightly allowed to bear the "Energy efficiency made in Germany" logo of the BMWi.
The flexible manufacturing system (FMS) enables low-manpower 24/7 production with a fully monitored machining process and seamless interaction of all internal and external systems, including the WaldrichSiegen diagnostic system, the high-pressure coolant system for single-lip drills and drill breakage monitoring as well as camera system and Omative performance monitoring. The fully automated pallet changing system consists of six external setup/buffer stations and a total of 8 pallets (4,000 x 4,500 mm) with a maximum load capacity of 100 t and is equipped with an automated guided vehicle (AGV). Both machines are connected to a common rack-type tool magazine with a total of 608 tool pockets, which is also prepared for automated tool loading and unloading via an automated guided vehicle (AGV).
WaldrichSiegen is executing the turnkey project for the highly complex production system as general contractor and will hand over the machines to the new customer plant in Parsdorf next year. For KraussMaffei Technologies, the start of production with the new ProfiMill will also mark the beginning of permanent energy and CO₂ savings in the production of injection molding machines.